Deep-drawn parts for the pharmaceutical industry and medical technology
Sector solutions for the pharmaceutical industry and medical technology
High-quality precision deep-drawn metal parts are an innovative solution for the pharmaceutical industry and companies in the medical technology sector. Deep-drawing technology, a metal forming process in which a sheet of metal is drawn into a mould, enables the production of complex and precise shapes in a wide variety of dimensions. The technology offers numerous advantages for manufacturers and end users in the pharmaceutical industry, from design flexibility to sustainability.
At Euscher, we are your thermoforming experts with many years of experience in the pharmaceutical industry and as a supplier to manufacturers of modern medical technology. Whether ferrules / crimp sleeves for asthma spray cans, sleeves for pressure reducers and pressure regulators on medical devices, metal housings for hearing aids or implant housings – we produce high-quality precision deep-drawn parts in bulk to your individual requirements.
Do you have an idea?
We find a solution. Together.
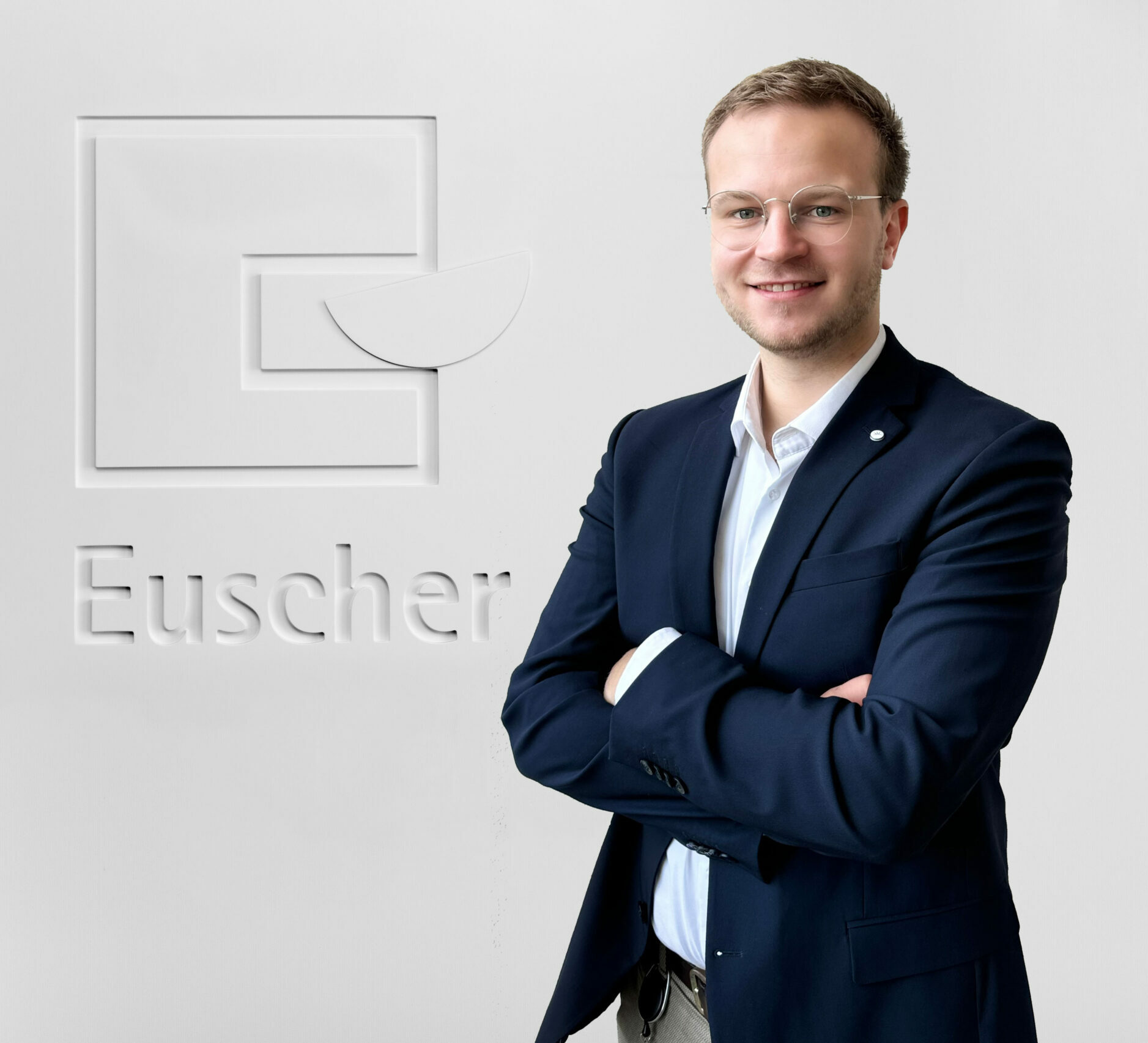
Jarid Asseburg
Key Account Management
Deep-drawn parts in the pharmaceutical and medical technology industries – the advantages
Sustainability and environmental friendliness
At a time when sustainability is becoming increasingly important, metal deep-drawn parts offer an environmentally friendly packaging option, for example for asthma sprays. The metals are fully recyclable and retain their quality so that new products of the same quality can be manufactured from scrap metal without the need to extract additional resources.
Cost efficiency
The durability and robustness of precision deep-drawn parts reduces the need for frequent replacements or complaints. In addition, the efficiency of the thermoforming process enables the mass production of parts at a lower cost, which can lead to an overall reduction in production costs.
Design variety and aesthetics
Deep-drawn metal parts allow a high degree of design flexibility, which is particularly important in the cosmetics industry, where the appearance of a product can be crucial to its success. With thermoforming technology, manufacturers can create unique, appealing shapes and designs that stand out from the competition. The ability to mould metal into complex geometries opens up new avenues for innovative packaging solutions and product designs that are not only functional but also visually appealing.
Durability and protection
Metal deep-drawn parts offer exceptional durability and robustness, ensuring that the medical device is protected from external influences such as pressure, temperature changes and moisture. This is particularly important for high-quality or sensitive pharmaceutical products that require additional protection to preserve their quality and effectiveness.
Pharmaceutical industry – a head start with deep-drawing technology
Deep-drawn parts offer a range of benefits to the pharmaceutical industry and companies that manufacture medical devices, from design flexibility to durability, protection and sustainability. Our technology enables manufacturers to develop innovative, attractive and functional components that meet today’s requirements for functionality, protection and environmental friendliness. This enables manufacturers to differentiate themselves in a highly competitive market.
Benefit from Euscher’s expertise, because we produce complex geometries for the individual requirements of the pharmaceutical industry in just one process and realise deep-drawn parts in a wide range of geometries and quantities from various materials.
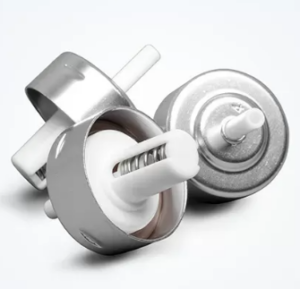
Innovative products and processes for the pharmaceutical industry
When it comes to precision deep-drawn metal parts and assemblies, Euscher has exceptional expertise. We have been proving our innovative strength and experience time and again for 100 years. We are also happy to develop individual products for you – or bring your specifications to series production in a structured manner.
Every large-scale production run is optimally tailored to your requirements. To achieve this, the Euscher team sometimes takes an unconventional technological approach: we can even produce highly complex geometries at high working speeds.
Creating new things together
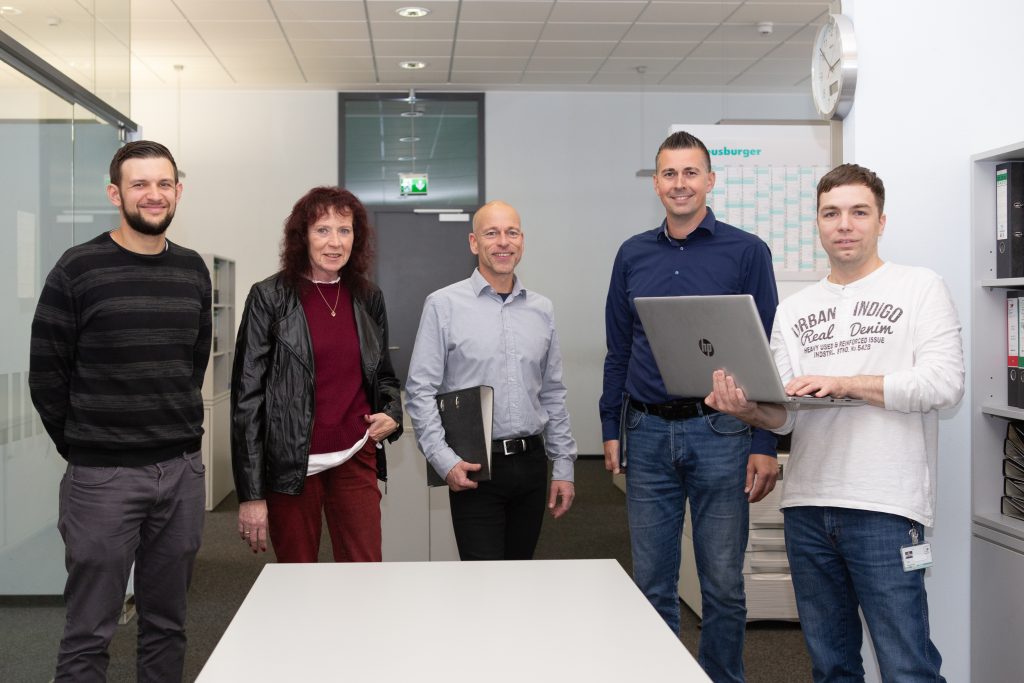
As an experienced supplier to the pharmaceutical and medical technology industry, we are also happy to support you with your new developments. We are curious about your visions: Take advantage of our many years of experience in the industry at an early stage so that we can realise your ideas together! We work in partnership with you to develop the optimum solution – a cost-effective product of the highest quality that is ideally suited to the desired application.
You can expect a service that is reliably and specifically tailored to your requirements. We are happy to explore the limits of what is possible and, where possible, we will exceed them for you.
To achieve this, we work hand in hand internally: In an integrated development process, our teams from sales, design, toolmaking, production and quality assurance get your innovations off the ground.